Туннель для пастеризации субстратов
Обработка субстрата в туннеле для производства грибов вешенки на данный момент является самой ресурсосберегающей технологией, обеспечивающей стабильное качество грибных блоков и высокую урожайность гриба.
Растительное сырье для туннельной технологии.
Сырьем для производства субстрата является многокомпонентная смесь соломы злаковых культур и сена (возможно с добавлением лузги).
Сначала смесь измельчается или расплющивается. Затем увлажняется вручную или с помощью вращающихся бочек — на фото справа. Складируется на площадке или в бункере, и после нескольких перекидок помещается в туннель для дальнейшей обработки.
Что такое туннель для пастеризации субстрата вешенки?
Туннель – это теплоизолированная камера, где подготовленное сырье обрабатывается паром (еще говорят -запаривается или пропаривается) – происходит пастеризационная обработка.
Затем следует охлаждение этой биомассы и она готова к инокуляции – засеву с мицелием в пакеты. Цель такой обработки сырья – уничтожение чужеродной микрофлоры (плесеней и бактерий) и частичное разложение растительной массы для лучшего развития мицелия вешенки. Постоянный контроль качества субстрата (содержание азота, влажность, рН) технологом на производстве, позволяет избежать брака и повысить урожайность.
Камера для пастеризации (пропарки) субстрата для вешенки (рис. 1) — это помещение, имеющее ворота с двух противоположных сторон – одни для загрузки сырья, другие – для выгрузки. Стены, потолок и дно должны быть теплоизолированы пенопластом или пенополиуретаном.
В камере имеется поддон, в который подается пар и сетчатый пол, на который грузится сырье. Пар рециркулирует через сырье по вентиляционной системе, в которой так же предусмотрена подача свежего воздуха и клапан сброса. Для исключения человеческого фактора и повышения стабильности качества обработки используется автоматизированная система управления технологическими процессами, происходящими в пропарочной камере.
Парогенератор для пастеризации субстрата вешенки.
Для производства пара применяется парогенератор – газовый или твердотопливный. Работает парогенератор не постоянно, включаясь автоматически в случае понижения температуры в туннеле ниже заданной. Применение парогенератора в грибоводстве не ограничивается туннелем. Он также применяется при стерилизации субстрата. Некоторые грибоводы применяют парогенератор для создания влажности в камере выращивания.
Рис.1. Конструкция тоннеля.
1-шахта приточной вентиляции; 2-фильтр микробиологической очистки воздуха; 4-элемент охлаждения воздуха; 3,5-регулирующие клапаны наружного и внутреннего давления; 6-заборный воздуховод рециркуляционного воздуха; 7-вентилятор; 8-диффузор; 9-камера статического давления; 10-щелевой пол тоннеля; 11-трубопровод подачи пара.
Туннель можно сделать разной вместимости от 2-3 тонн до 50 тонн субстрата. Для производства необходимо помещение от 100 до 230 кв.м., в зависимости от количества производимых грибных блоков. В высоту оно должно быть около 6 м (хотя бы в той части, где будет расположен туннель) и навес для предварительной подготовки субстрата не менее 100 кв.м.
В случае загрузки 20-ти тонного туннеля раз в 8 дней можно произвести субстрат для выращивания 20 тонн гриба в месяц, при загрузке раз в 4 дня, соответственно — для выращивания 40 тонн вешенки в месяц.
Для изготовления грибных блоков используются гидравлические прессы.
Необходимое оборудование:
Соломорезка
Вращающаяся бочка для замочки (желательно)
Парогенератор
Транспортеры или трактор с грейфером (вилами – захватом)
Гидравлический пресс-формовщик блоков
Вентиляционное оборудование и автоматика управления процессами в туннеле
Вентиляционное оборудование чистой зоны
Водогрейный котел для обогрева цеха и нагрева воды для процесса замочки растительного сырья
Минитрактор для выгрузки субстрата в чистой зоне (желательно).
Сырье для изготовления субстрата измельчается на соломорезке. Фракция соломы и сена для блоков вешенки — это стебли, порубленные на участки 5-10 см. Такая фракция способствует определенной степени пружинистости субстрата, и он не слеживается. Нужно следить, чтобы сырье не измельчалось в пыль, при этом оно переувлажняется и/или плохо пропаривается. Кстати, именно по этой причине при пастеризации не применяют опилки.
Субстрат сначала необходимо замочить.
Можно сделать это вручную — сформировать слой растительного сырья (как правило, используется солома любых злаковых культур, шелуху подсолнечника, сено бобовых) высотой не более 70 см. И замочить его водой из шланга, одновременно протаптывая. Затем засыпать следующий слой и проделать тоже самое. На этом этапе в субстрат вносится известь или сода. Как рассчитать ее количество — смотрите здесь.
Можно использовать бочку (на фото вверху), которая вращаясь орошает порцию соломы.
Затем субстрат должен напитаться влагой, на это уходит не менее суток. Споры, которые есть в субстрате за это время успевают набухнуть и проклюнутся. Почему это важно — смотрите в этой статье.
Если вы замачиваете сырье дольше суток, его необходимо обогащать кислородом — например путем перекидки.
Перед тем, как загрузить сырье в туннель, измерьте влажность (экспресс-метод — в конце статьи) она должна быть не ниже 74 и не выше 76%.
Загружаем подготовленное сырье в тоннель.
Можно в ручную, можно использовать телескопический транспортер.
И в том, и в другом случае главное требование — равномерность и быстрота забуртовки. По высоте загрузка должна быть не менее полутора метра. Верхний предел загрузки — не более 2,3-2,4 м связан с тем, что нужна хорошая продува слоя вентилятором. Субстрат во время пропарки может осесть. Между слоем сырья при закидке и потолком туннеля должен быть разрыв не менее 80 см.
Засыпая субстрат, рабочие вставляют в пазы за воротами доски, формируя фальш-стенку. Кликните для увеличения:
Процесс пастеризации.
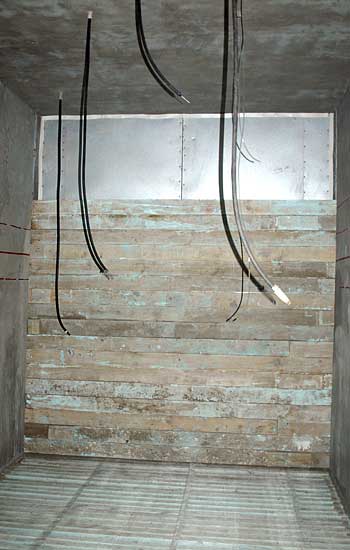
После загрузки закрывают ворота. Сначала включают вентиляцию для выравнивания температуры в толще субстрата — за время заполнения туннеля масса саморазогревается. Температуру отслеживают по датчикам.
Когда она выравняется, в систему вентиляции начинают подавать пар. Парогенератор для туннеля выбирается в зависимости от тоннажа. На 10ти тонный туннель достаточно 150 кг пара в час.
Количество воздуха — 250 кубометров/в час.
Температуру держат 69-73 град. Почему именно такую — смотрите здесь.
По времени обработки — не менее 18-22 часов в зависимости от состава и состояния сырья.
Все процессы в туннеле можно и желательно автоматизировать. Программу автоматического управления режимами в туннеле можно приобрести, созвонившись с менеджером нашего представительства, в зависимости от страны, где вы живете.